US Army inches closer to 3D-printing spare parts under fire
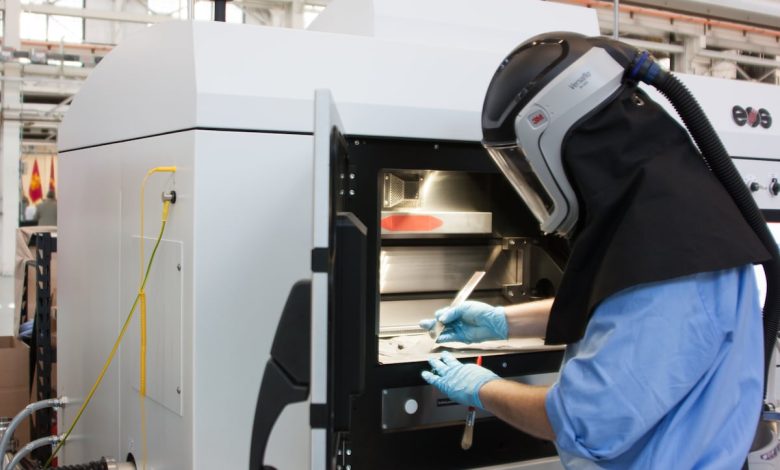
Army officials are pushing to add new 3D models to a repository of data files that troops can one day use to print spare parts close to the front line, according to a senior service official.
During a recent rotation at the Joint Readiness Training Center at Fort Johnson, Louisiana, a team from the Army’s Tank-Automotive & Armaments Command passed a digital file of a repair part to a team that printed the replacement at the tactical edge.
“That was a heavy lift and we don’t have it right yet,” Lt. Gen. Christopher Mohan, Army Materiel Command’s deputy and acting commander, told Defense News, “but we know that we can do it now.”
The effort was a part of Army Chief of Staff Gen. Randy George’s vision of transforming how the service fights and adapts in the heat of battle.
While the Army has tried 3D printing at the tactical edge, which describes units closest to combat, it has previously come with a large footprint such as an entire trailer.
Officials at Army Materiel Command have started 3D-printing more parts because supply chains are still strained from the coronavirus pandemic, Mohan explained, and because of “exponential growth” of requirements coming primarily out of units in Europe.
AMC has begun using more advanced manufacturing techniques to make widgets that are no longer under contract or which the original contractor no longer stocks. “We’re targeting those parts,” Mohan said. “If we have the tech data, it’s relatively easy to map it and then load it into a digital repository.”
If the Army doesn’t own the data, it has to reverse engineer it and run the part through a first article test just like it would a brand new part, Mohan noted.
The command, back in 2020, came up with an overarching strategy for how it wanted to tackle 3D printing and additive manufacturing across the force, establishing a hub of manufacturing capability at Rock Island Arsenal, Illinois, along with 25 other various depots, plants and arsenals in support.
While the repository is still a nascent capability, the Army has about 1,000 parts mapped and loaded in it and is finding that some of the parts are improvements over what original equipment manufacturers provided.
“The long-term vision is that we have this centralized hub of data and then we map both the [organic industrial base] and other capabilities all the way down to the tactical level and say, ‘Okay, we can see what type of machinery we have at each one of our depots and arsenals and then all the way down to the tactical level,” Mohan said. “And the units at the tactical level will be able to access the data based upon the capability that they have.”
The Army does not want a unit with very nascent 3D printing capability to try to make complex parts, Mohan cautioned, so “we’ve got to get the control measures in place and we’re working on that.”
The Sustainment Center of Excellence is working with AMC to enhance training of the soldiers who are doing advanced manufacturing at the tactical level as well, Mohan noted.
For the fan shroud replacement part printed in the field at Fort Johnson, it was “a very simple part,” Mohan said, but when using titanium, some parts the service wants to print can take roughly four days to complete.
“We don’t expect that capability is going to be down at the tactical level,” he noted.
“We’re having discussions about the future, where [is] that tactical capability best suited for an expeditionary Army? Is it down at the brigade level? Is at the division level or the corps level? I think it depends on what we’re going to try to accomplish from repair parts printing,” Mohan said.
AMC is also making improvements to some of its parts manufacturing processes using additive manufacturing capability at the Joint Manufacturing and Technology Center at Rock Island, Arsenal, according to Mohan.
“We’re using 3D printing and advanced manufacturing techniques to make us faster in forgings and castings,” he said. Casting molds are typically made with sand using a wood mold to shape the sand mold, which can take weeks, Mohan explained. “Now we’re 3D printing molds with an advanced material that’s heat resistant.”
The Army has “shaved weeks off of parts and castings by integrating advanced manufacturing techniques into our existing processes,” he said.
Jen Judson is an award-winning journalist covering land warfare for Defense News. She has also worked for Politico and Inside Defense. She holds a Master of Science degree in journalism from Boston University and a Bachelor of Arts degree from Kenyon College.
Read the full article here